Technical Center
Welcome to the RPS Technical Center. The purpose of this series is to provide you with a more technical view of FRP piping systems, and the many considerations involved in a successful design. If you’re not familiar with engineered pipe, we suggest you read the articles in sequence; the more familiar can start anywhere.
Readers who complete the articles will have a broader understanding of and appreciation for pipe systems designed by RPS, and a great level of confidence in the pipe we manufacture. If you have any questions, please contact us.
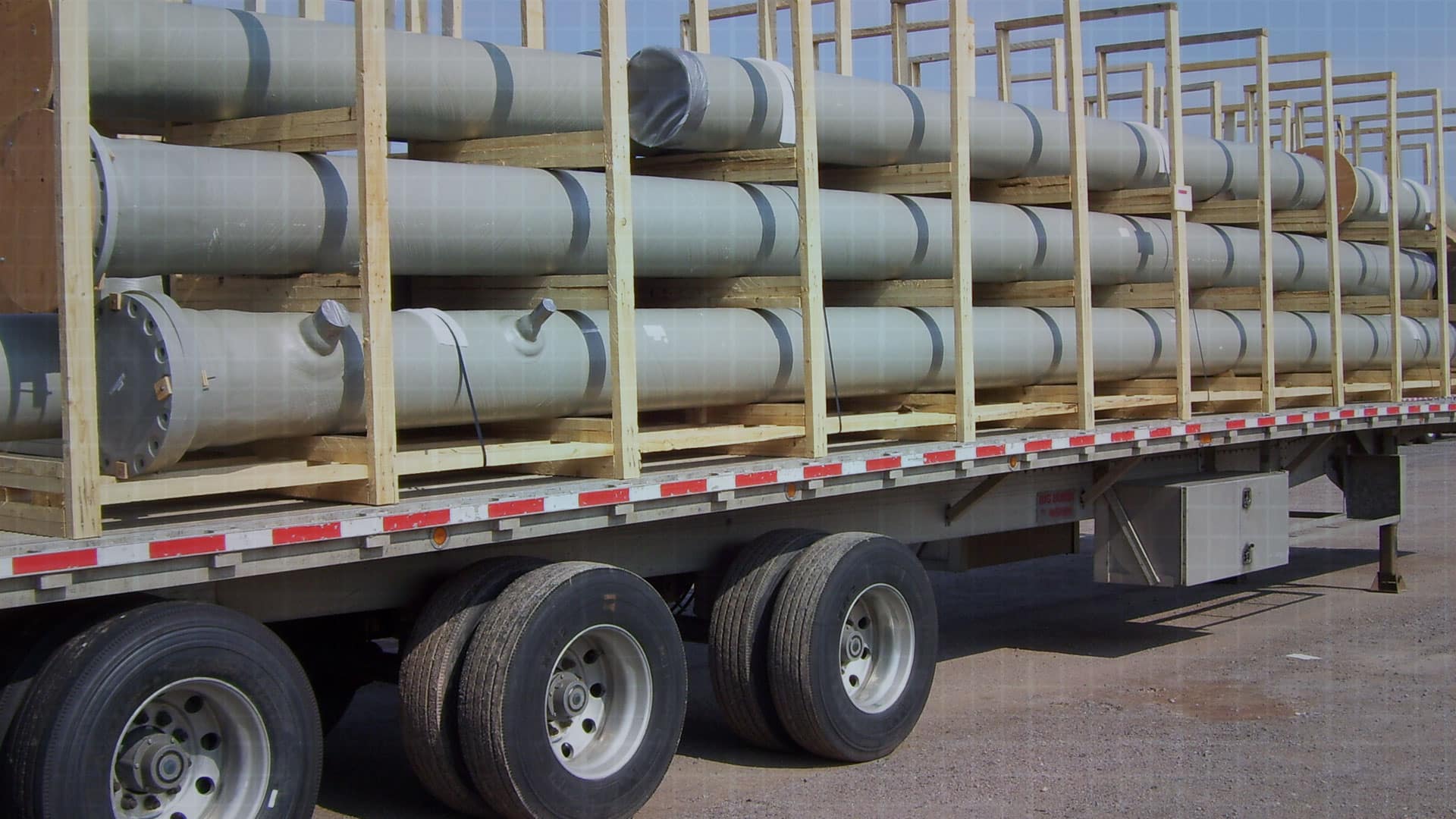
The RPS Chemical Resistance Guide
We’ve developed a number of piping systems, which have been designed to provide outstanding resistance to a wide range of chemical environments. Download our Guide to explore the RPS family of HPPE (High Performance Pre-Engineered) piping systems.
Reach out for more information about the wide variety of products and operational expertise RPS offers our customers.