Supply chain resilience has been cemented as a critical cornerstone of business continuity
The FRP Industry is projected to reach a market value of $5.69 billion by 2028
In the shadow of an evolving global landscape, the Fiberglass Reinforced Plastic (FRP) industry has emerged not only intact but invigorated, projected to reach a market value of $5.69 billion by 2028. This growth is a testament to the material’s remarkable benefits: durability, low maintenance, and resistance to corrosion. However, beneath this robust expansion lies a critical lesson unveiled by the COVID-19 pandemic—the undeniable value of localized manufacturing.
Learnings from the Impact of COVID-19 on Global Supply Chains
The pandemic’s onset sent shockwaves felt by all of us throughout global supply chains as we experienced disruptions to the flow of materials and finished goods. These disruptions highlighted a crucial reality: the ability to adapt is key to survival.
Supply chain resilience, once an afterthought, has been cemented as a critical cornerstone of business continuity.
The Advantages of Localized Manufacturing
Localized manufacturing emerged as a beacon of stability amidst the chaos. By minimizing reliance on distant suppliers, companies can better manage production schedules, mitigate logistics challenges, and respond swiftly to market demands. Our company, which operates solely out of North America, was — and continues to be — uniquely positioned to support our localized customers during times of potential challenges and disruptions.
Speed to Market in a Competitive Landscape
Every day, the race to market continues to accelerate for our business as well as our clients’, and uncertainty in the supply chain of critical components will be crippling. In this increasingly competitive landscape, the ability to move quickly from concept to commercialization is not just advantageous—it’s imperative. Localized manufacturing compresses the timeline, enabling companies to pivot rapidly and capitalize on emerging opportunities.
The Rising Costs of Global Shipping and Tightening Margins
Beyond agility, the economic argument for localized manufacturing has grown stronger. Skyrocketing shipping costs have eroded margins, turning the gaze of businesses towards more sustainable and cost-effective production models. Local manufacturing stands as a bulwark against these financial headwinds, offering a more predictable and leaner cost structure.
Case Study: Speed to Solution and Installation Support Enabled by Localized Manufacturing
A significant case involving an electric utility in the United States demonstrated the strategic advantage of localized manufacturing and bespoke engineering solutions. The utility was grappling with the failure of rubber-lined carbon steel pipes in their pollution control equipment. The pipes were essential for the wet limestone flue gas desulfurization (FGD) process, designed to remove sulfur dioxide from flue gases in a coal-fired boiler.
The rubber-lined steel pipes were degrading prematurely, causing operational issues and high maintenance costs. The plant’s leadership needed a rapid and durable replacement solution. It was at this juncture that RPS Composites’ localized manufacturing capabilities and technical expertise came to the fore. After evaluating various options, the plant chose RPS Composites’ “A” series erosion/corrosion-resistant FRP pipe for its proven performance and cost savings.
The pipe and fittings, constructed using a fire-retardant vinyl ester resin, were tailored to withstand the corrosive and abrasive nature of the limestone slurry. The design was based on extensive stress analysis and adhered to stringent ASTM standards, ensuring durability and reliability. RPS Composites also provided comprehensive installation support, which was crucial for the proper execution of the project. The RPS team conducted inspections and quality assurance of the FRP field joints, ensuring that the newly installed pipes met all specifications and performance expectations. Not only did the transition to RPS Composites’ FRP pipes resolve the immediate issue, but it also promised over twenty years of maintenance-free service, illustrating an excellent return on investment for the utility. This case study exemplifies the tangible benefits of speed to solution and installation support, showcasing how RPS Composites’ localized manufacturing approach delivers long-term value and reliability to clients.
The Winning Combination
This case is a clear illustration of how localized manufacturing, coupled with technical acumen and customer-centric service, creates a competitive edge. In a world where production delays and logistical challenges can result in significant financial repercussions, the ability to provide rapid and reliable solutions is invaluable. RPS Composites stands as a testament to the efficacy of this approach, reinforcing the premise that localized manufacturing is not just a reaction to past challenges but a proactive strategy for future success.
Call to Action
The time for transition is now. We invite businesses to join us in embracing the many benefits of localized manufacturing.
Let us know how RPS Composites can help you with your next project. We’re here, ready to share our expertise and experience to foster a more resilient industrial ecosystem, driven by innovation in FRP manufacturing.
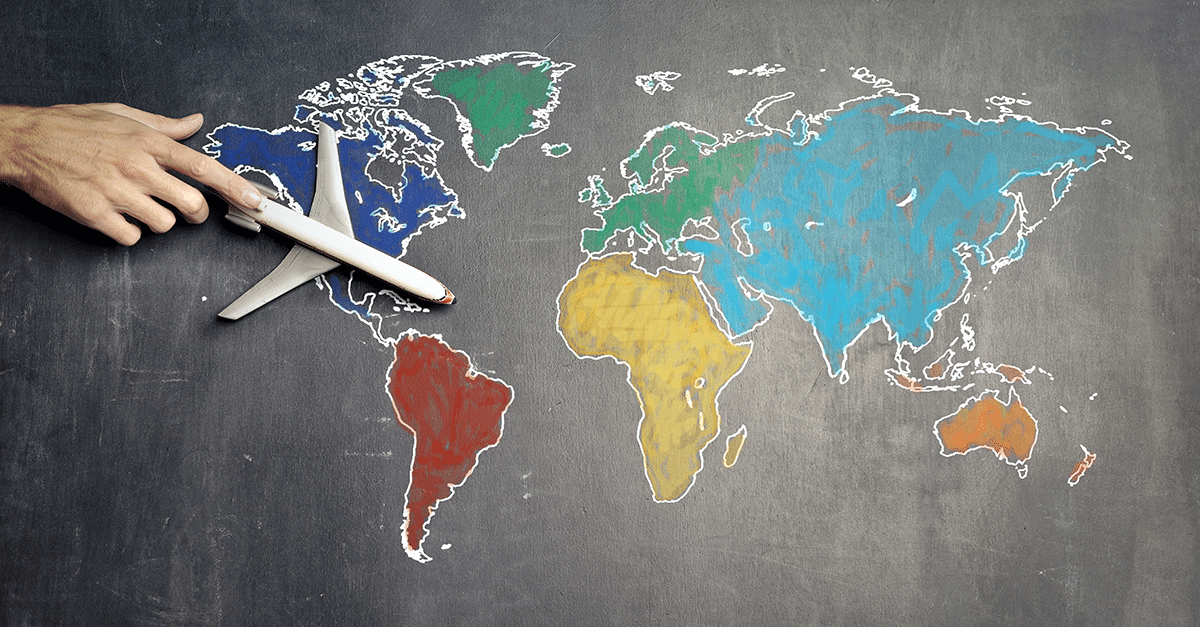
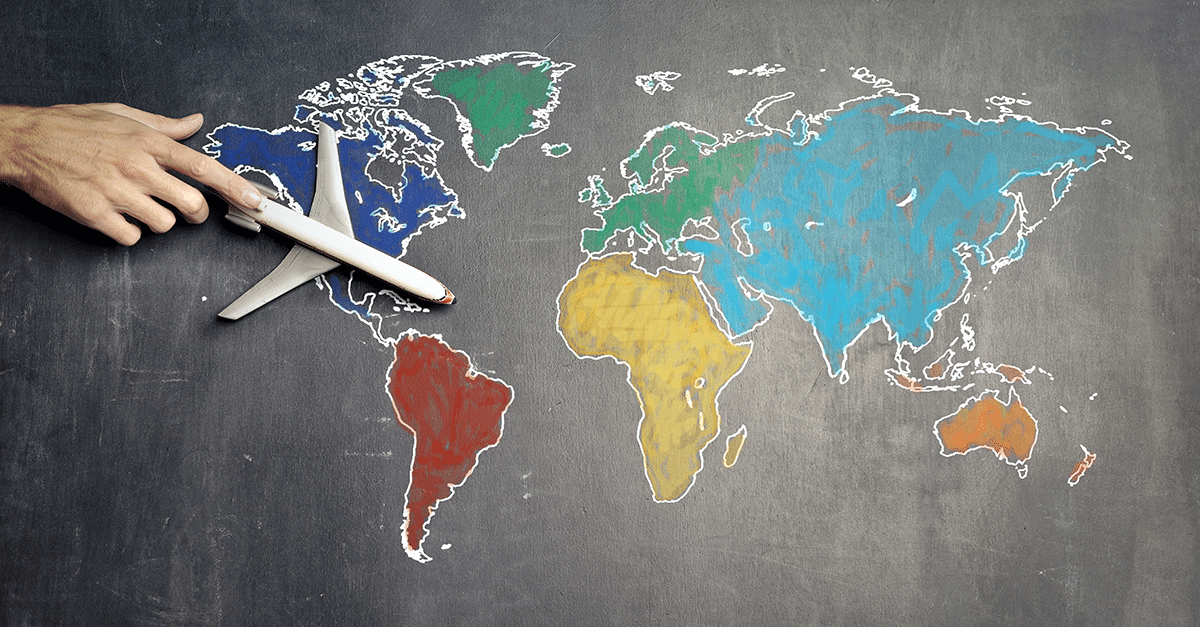