Fiberglass Reinforced Plastic (FRP) pipe is resistant to a wide range of chemicals and temperatures. Many types of corrosion attack that are harmful to steel pipe have no effect on FRP, including aerobic, galvanic, pitting, intergranular, and general corrosion.
However, FRP is subject to chemical attack through oxidation, pyrolysis (chemical decomposition at high temperature), hydrolysis (chemical decomposition in the presence of water), and solution attack. The resistance of FRP to these forms of attack relies primarily on the resin used in the corrosion liner.
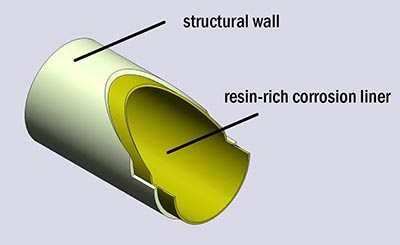
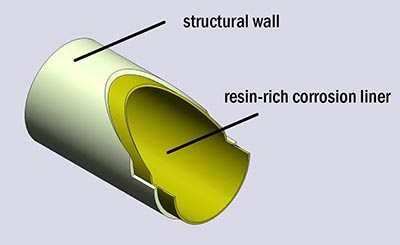
Typical FRP pipe construction
Other factors such as cure, liner construction, reinforcement type, and fabrication methods can also affect pipe performance. However, choice of the appropriate resin is the most critical factor in long term performance. RPS custom designs piping for specific applications with careful consideration given to resin selection. Making the right choice depends on a number of resin properties, including:
- Chemical Resistance
- Heat Distortion Temperature
- Tensile Strength and Modulus
- Flexural Strength and Modulus
- Elongation @ Break
- Processability
Resin manufactures supply information about the chemical resistance as well as physical and mechanical properties of the resins, and RPS uses this information, in conjunction with over 30 years of fabrication experience, to develop a laminate specification for each application. There are several polyester and vinyl ester resins suitable for pipe fabrication. The most commonly used are:
- Bisphenol Epoxy Vinyl Esters
- Epoxy Novolac Vinyl Esters
- Bisphenol Fumarate Polyesters
- Isophthalic Polyesters
By custom designing pipe systems, RPS can make a resin selection for each application that takes into consideration the unique properties of the resin and the cost implication associated with the raw material price and resin processability. Since the right corrosion liner is critical to your project, this is not a one-size-fits-all solution; it pays to customize your design to your needs. The wrong liner, at best, leads to cost overruns, at worse, can mean premature failure and injury.
The resins listed offer resistance to a wide range of chemical media. Typical applications include:
- Black Liquor
- Brown Stock
- Chlorine Dioxide
- Chlorine Gas
- Chlorine Water
- De-ionized / Demineralized Water
- Ferric Chloride
- Green Liquor
- Gypsum Slurry
- Hydrochloric Acid to 37%
- Limestone Slurry
- Magnesium Chloride
- Nitric Acid to 20%
- Paper Mill Effluent
- Phosphoric Acid
- Plating Solutions
- Salt Brine
- Sodium Chlorate
- Sodium Hydroxide
- Sodium Hypochlorite to 18%
- Solvent Extraction Solutions
- Sulfuric Acid to 75%
Dual Laminate Piping
When the service conditions fall outside the acceptable criteria for FRP then our Dual Laminate piping solution may be considered.
We carry a full line of thermoplastic liners, including Polypropylene (PP), High Density Polyethylene (HDPE), Polyvinyl Chloride (PVC), Chlorinated Polyvinyl Chloride (CPVC), Polyvinylidene Fluoride (PVDF), Fluorinated Ethylene Propylene (FEP), Perfluoroalkoxy (PFA), and Ethylene Chlorotrifluoroethylene (ECTFE).
The vinyls (PVC and CPVC) are chemically bonded to the outer fiberglass structure with a bonding resin.
The olefins and fluoropolymers (PP/HDPE/PVDF/FEP/PFA/ECTFE) are bonded with a glass backing layer melt bonded into the liner, followed by a filament wound (standard) or hand lay-up vinyl ester fiberglass structure yielding a totally bonded dual laminate. This proprietary bonding process sets RPS Composites apart from other dual laminate suppliers, and in many conditions, makes our dual laminate the better choice over lined steel.
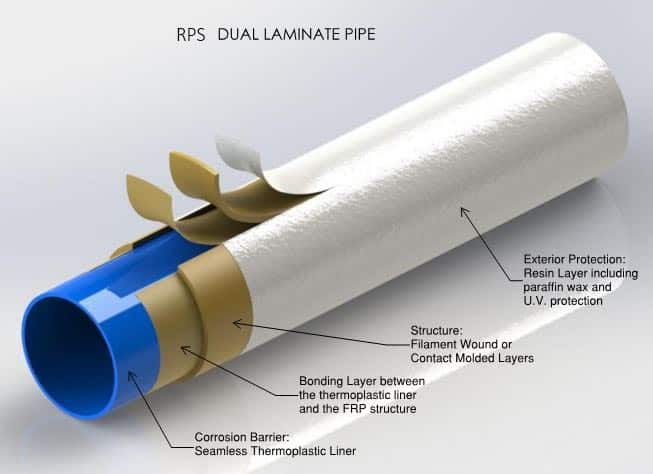
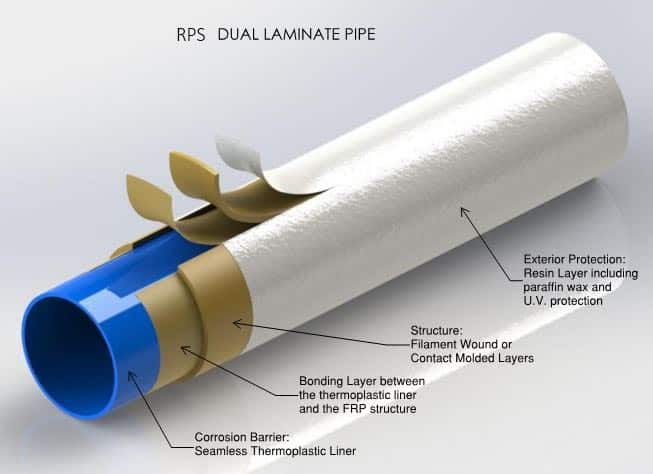
RPS Composites’ proprietary dual laminate construction
RPS has been custom designing FRP systems for more than 30 years. Between the FRP and Dual Laminate material options, we will make a product recommendation which is most cost effective for the desired service life of the system. The excellent corrosion, abrasion, and chemical resistance of RPS FRP piping systems have led to their application in many process industries including:
✓ Pulp & Paper
✓ Chemical
✓ Chlor-alkali
✓ Mining & Mineral Processing
✓ Flue Gas Desulphurization
✓ Water and Waste Water Treatment
✓ Fertilizer
✓ Power Generation
✓ Pharmaceutical
✓ Steel Processing
When it comes to corrosive fluid handling, storage, and infrastructure, industrial customers turn away from commodity pipe and turn to RPS Composites as their trusted advisor.