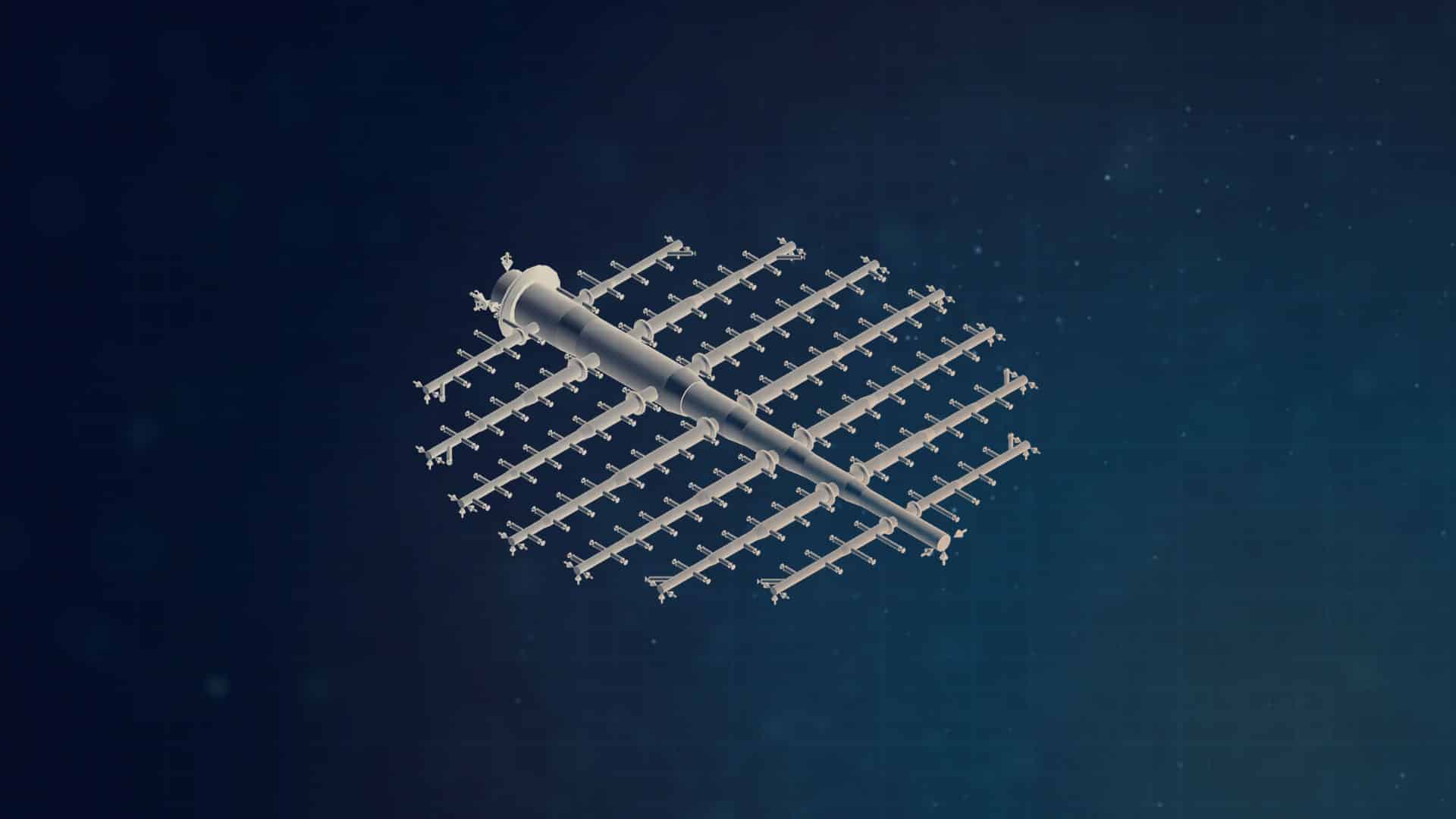
FRP Engineering Expertise
Customers rely on our FRP engineering expertise to deliver composite solutions for critical process piping, tanks and vessels, and custom equipment applications. In the corrosion industry failure is not an option, and with over 50 years of successful experience specifying and designing corrosion resistant composite equipment, we help customers realize the full benefits of fiberglass reinforced plastic (FRP) and dual laminate materials, thereby increasing the availability and reliability of their processing facilities. When performance counts, experience matters.
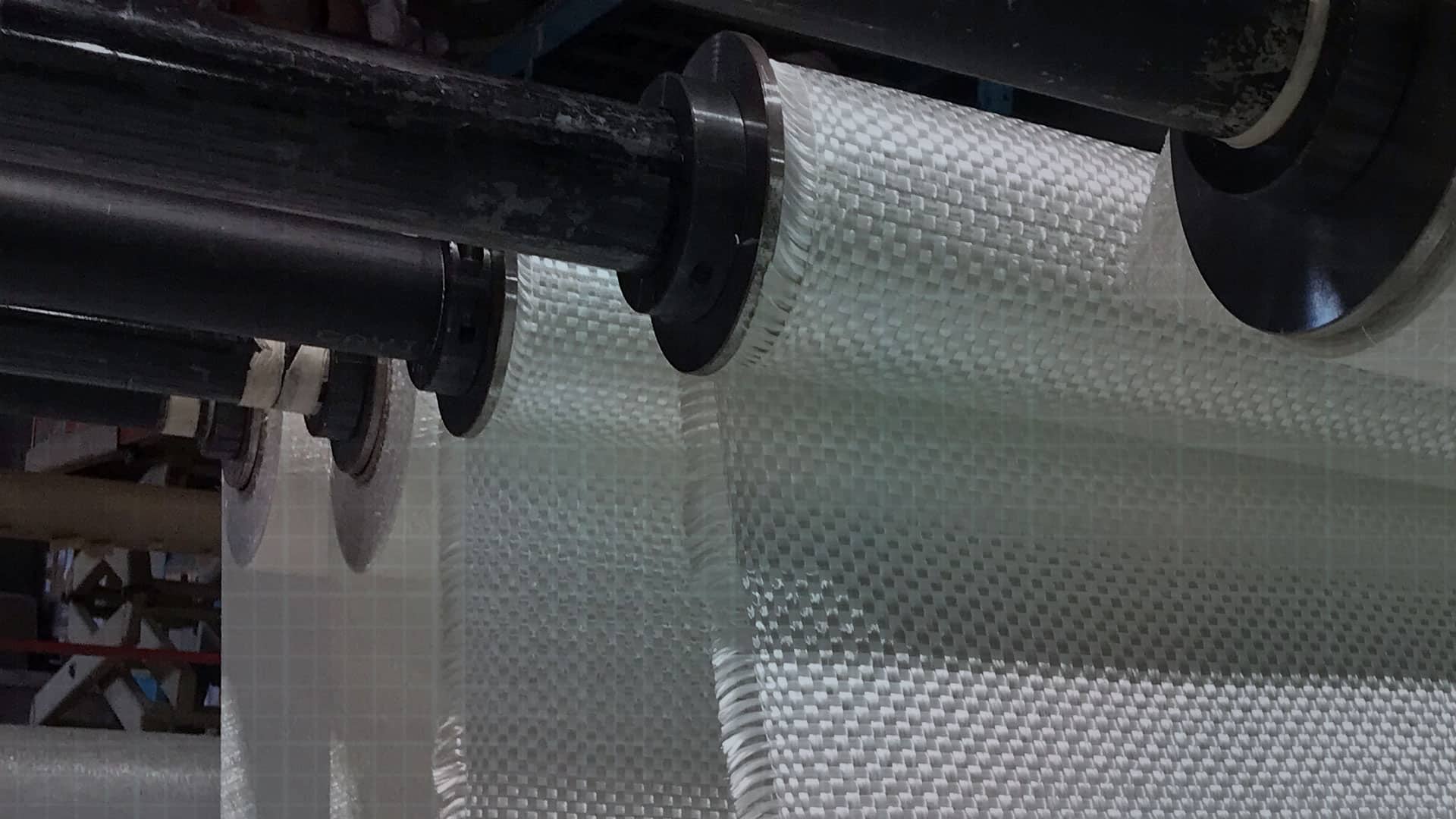
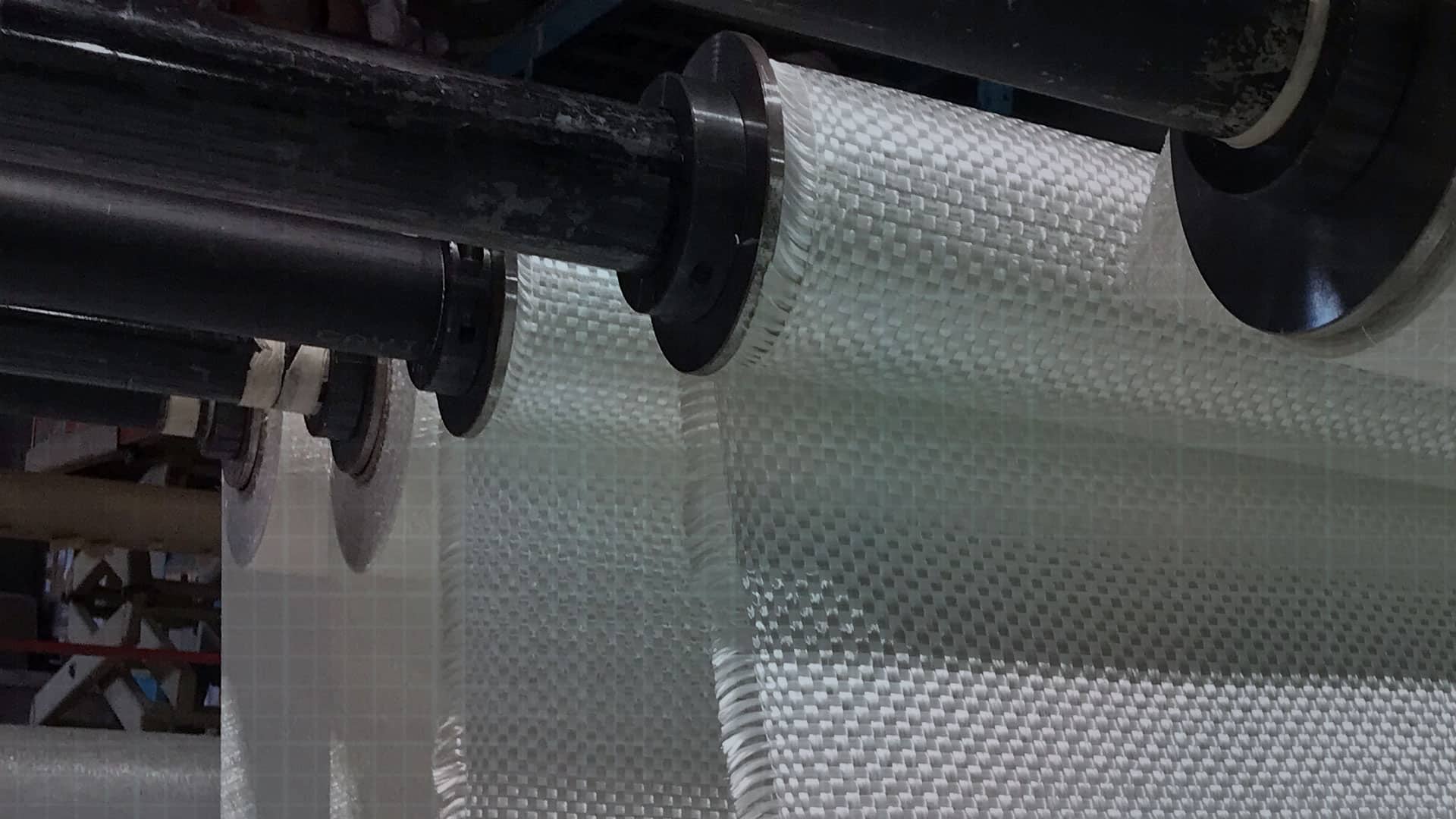
Material Selection
Industry spends billions of dollars every year replacing corroded steel pipe and equipment with like materials. However, corrosion resistant composite pipe systems and equipment are often better choices with lower life cycle costs. RPS designs and manufactures pipe systems and equipment with FRP and thermoplastic-lined FRP materials which can provide customers more reliable and cost-effective choices for their critical process systems. Not familiar with composites? Not a problem. Contact us with your process conditions and we will recommend the best choice for your application, ensuring proven state-of-the-art materials are incorporated into your equipment. By providing smarter choices we help customers realize the full benefits of composite equipment.
Our Engineering department has created a Technical Center to provide you with a more technical view of FRP piping systems, and the many considerations involved in a successful design.
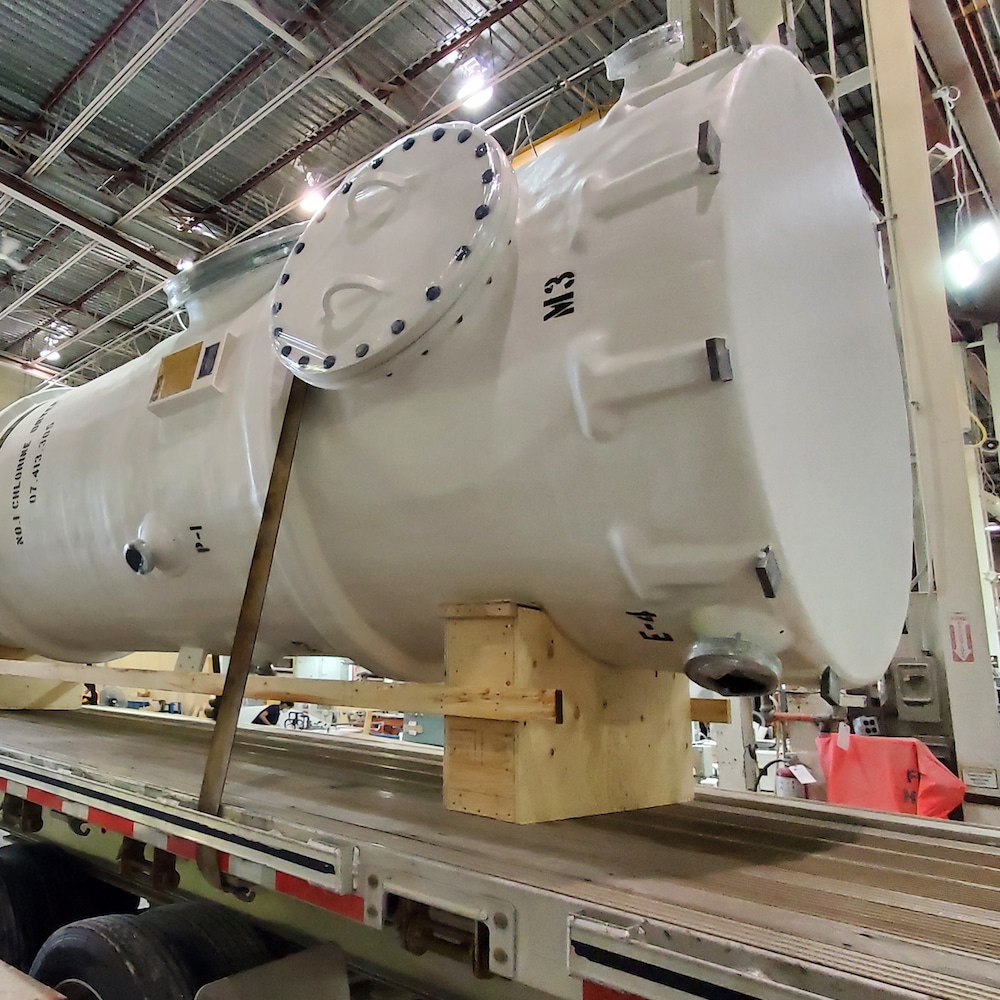
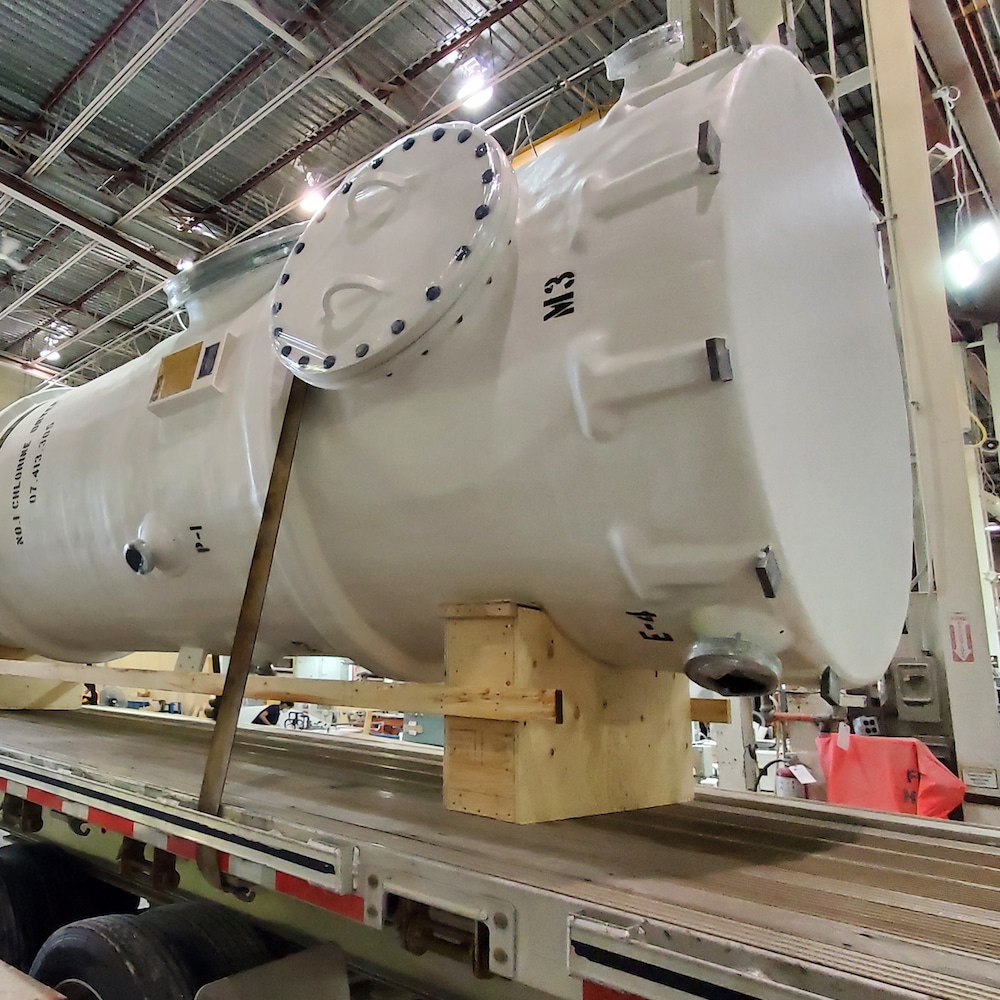
Performance Specifications
Need help developing a performance specification for your process vessel or pipe system? Not familiar with composites? We can help. RPS Engineering works with customers to develop specifications for vessels and pipe systems that reference current and relevant industry codes, standards, and practices. Performance specifications written around your service conditions and expectations leads to optimized design and performance.
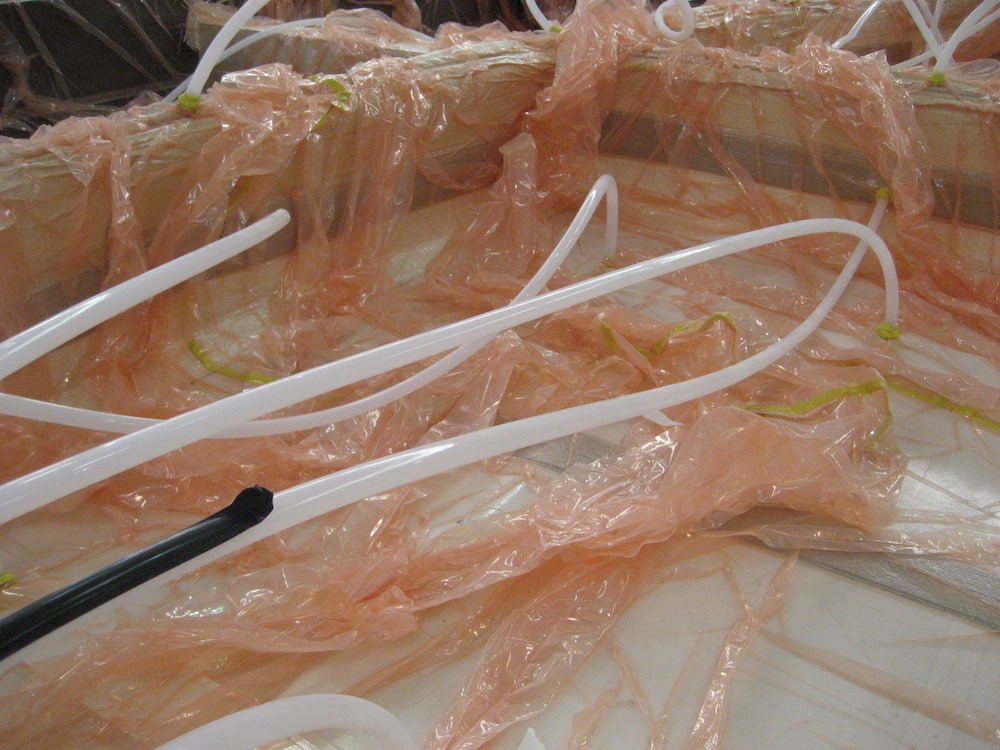
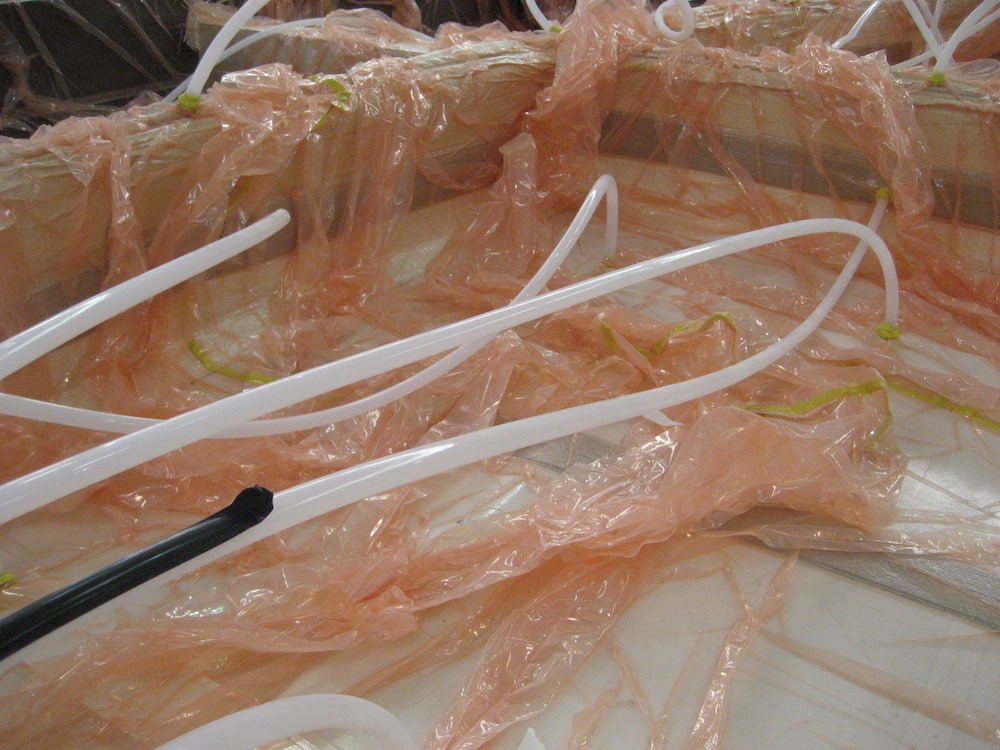
Component and Equipment Design
Composite materials are the best choice for many process applications, but material selection alone will not ensure success. Proper mechanical design is required to ensure equipment and components are capable of carrying all design loads with appropriate design factors. In addition, they need to meet the requirements of performance specifications, codes, and standards.
Our dual laminate and FRP engineering expertise arises from working to a variety of International Standards including:
- American Society of Mechanical Engineers (ASME B31.1, B31.3, RTP-1, NM.2)
- American Society for Testing and Materials (ASTM)
- American Water Works Assoc (AWWA)
- National Bureau of Standards (NBS)
- British Standards Institution (BSI)
- American Society of Civil Engineers (ASCE)
RPS engineering has over 50 years of success in designing FRP and dual laminate equipment and pipe system components to meet the critical reliability requirements of our customers.
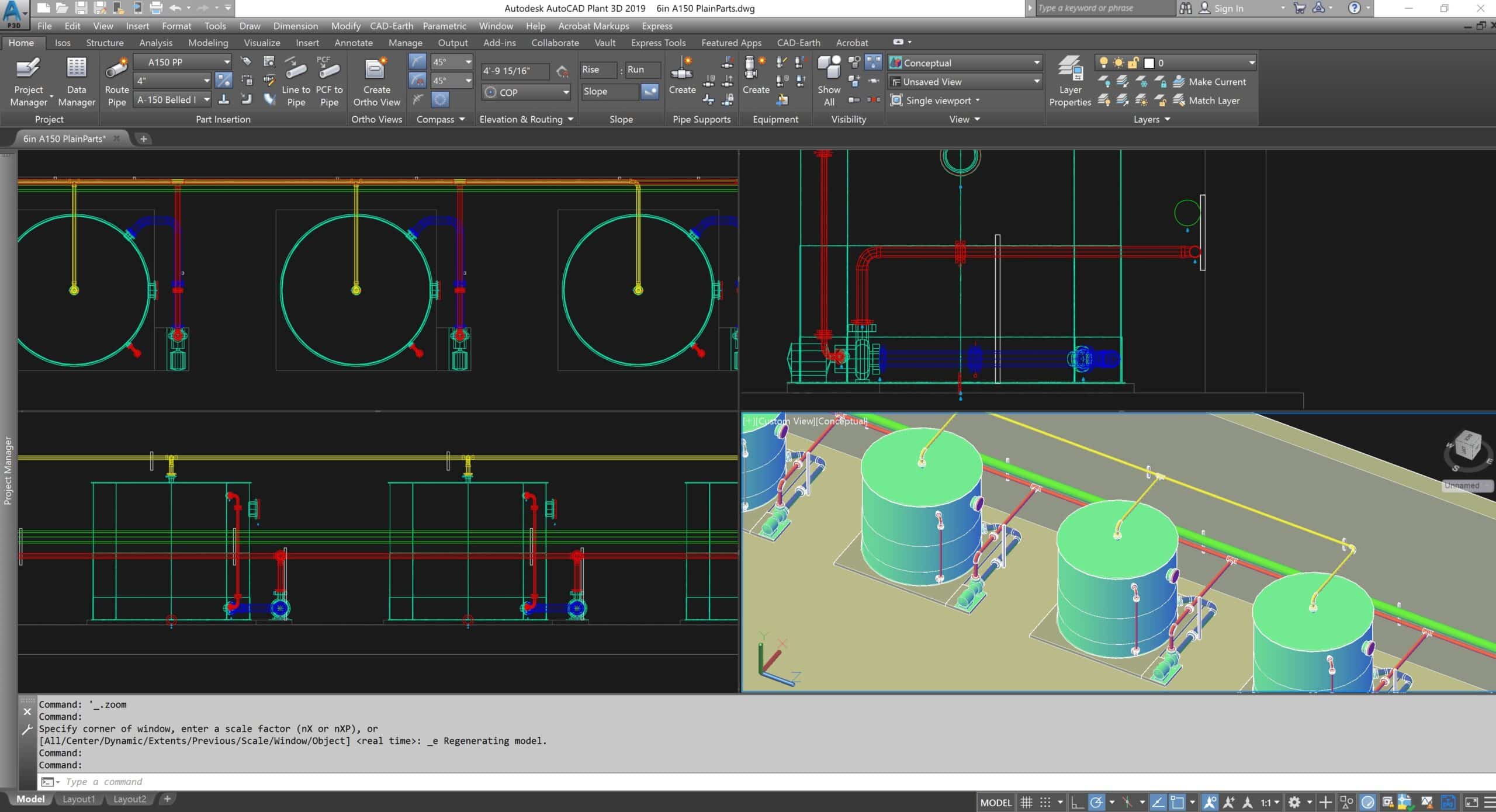
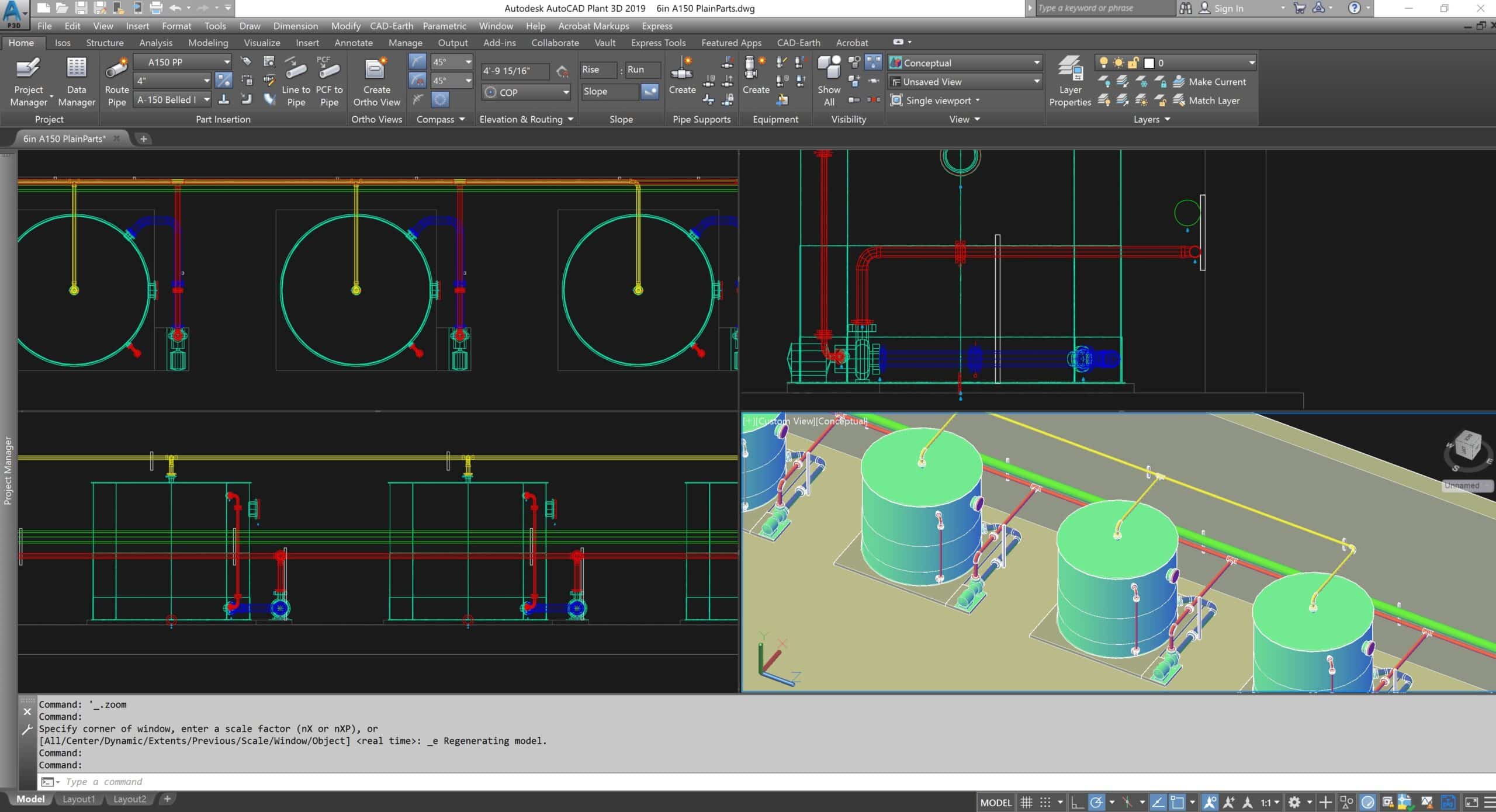
Drawings and 3D Models
Detailed and accurate equipment and pipe spool drawings help ensure RPS products meet customer requirements and facilitate installation.
Our AutoCAD Plant 3D Library is now available for download. This includes belled pipe and fittings 1” to 12”, and plain end pipe and fittings 1” to 60” for our A-150, P-150, and H-150 lines. If you need any assistance, or if you are interested in the Hexagon/Integraph Smart Plant 3D, Aveva E3D, or other pipe and fitting library formats, please contact us.
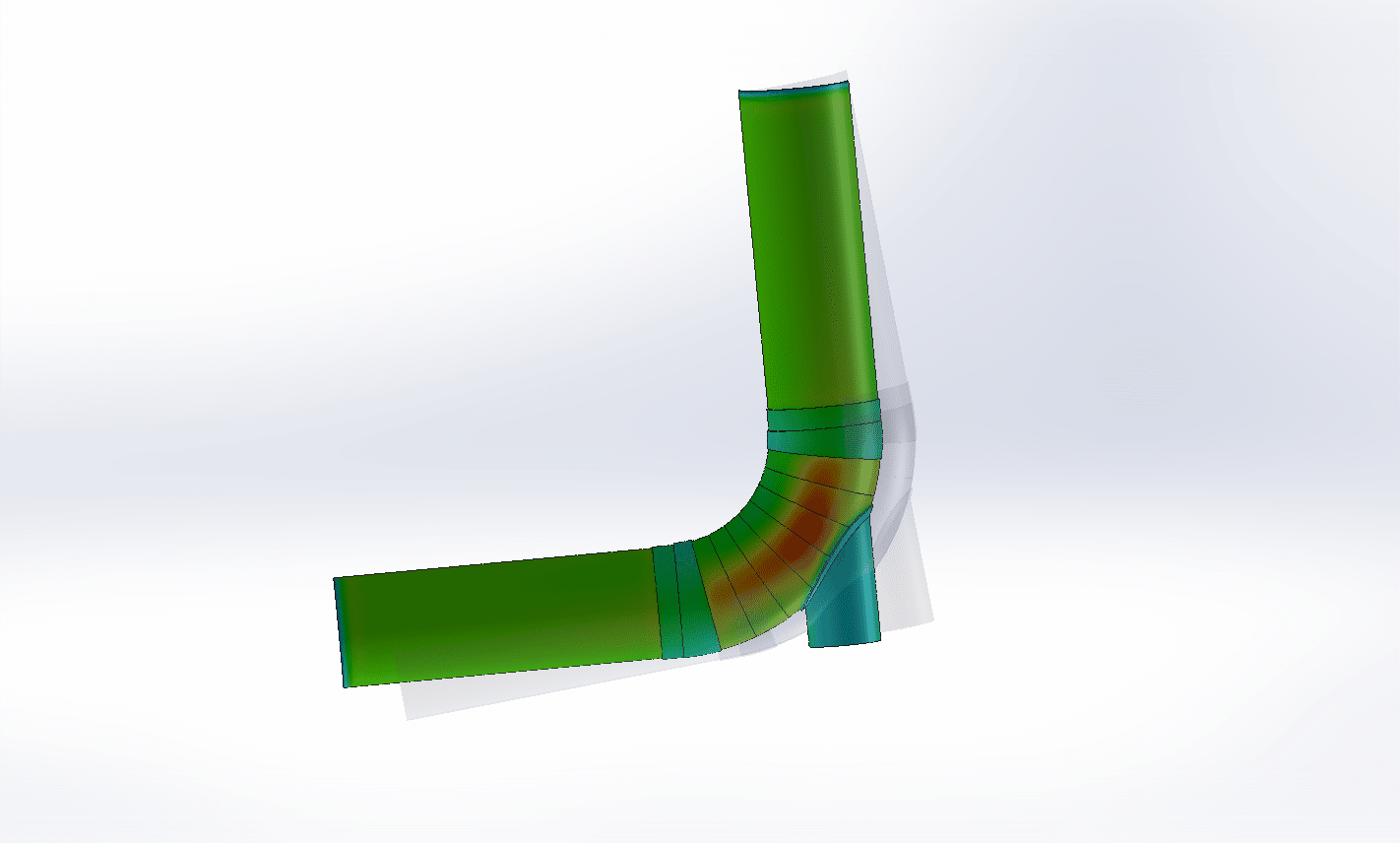
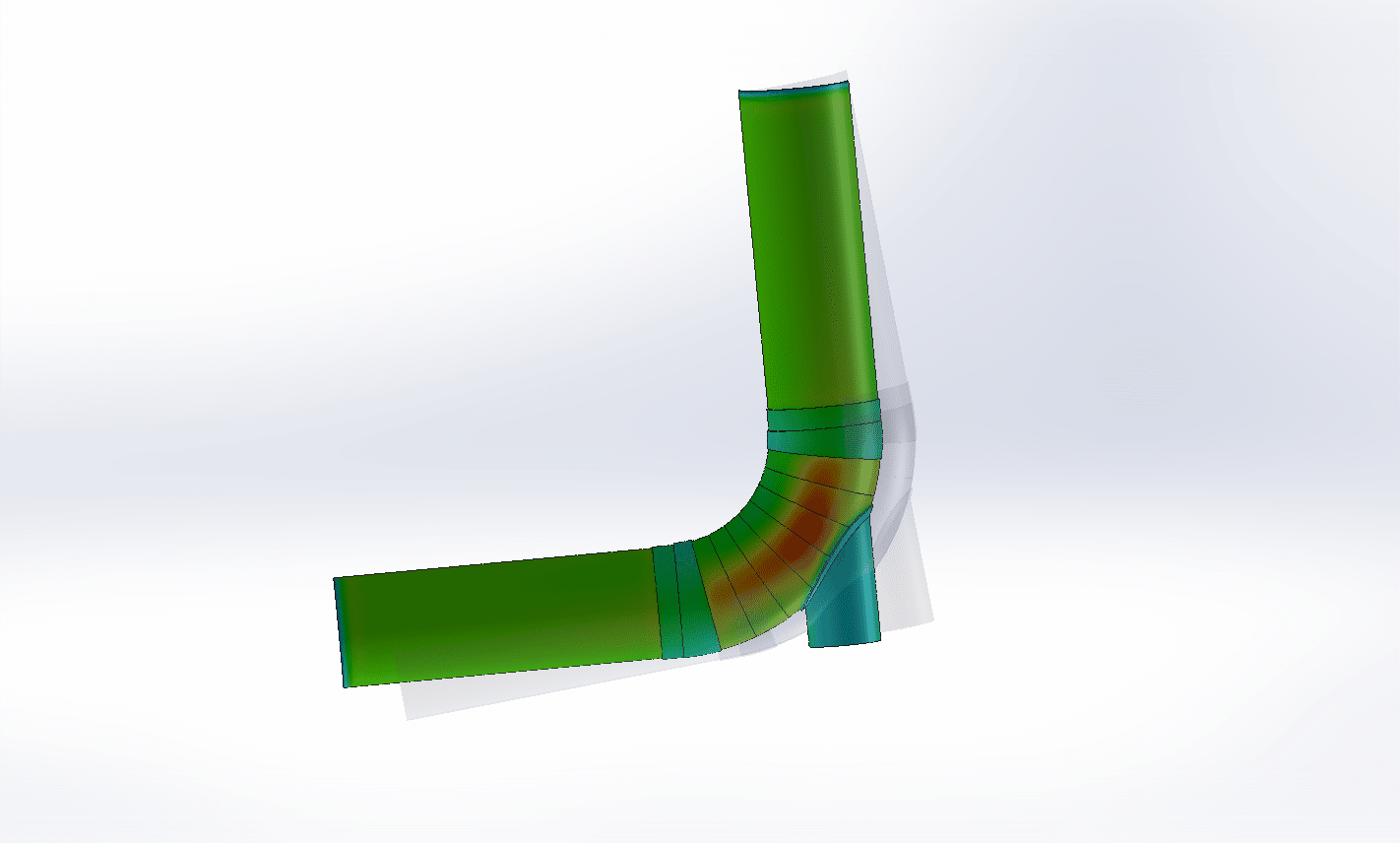
Pipe System and Equipment Stress Analysis and Finite Element Analysis
RPS offers PSA and FEA to ensure installed products perform as expected. Decades of FRP engineering expertise results in optimized designs for each application. Using the latest design and drafting software (CAESAR II Pipe Stress Analysis, Simulation and Nastran Finite Element Analysis, Trilam, AutoCAD, SolidWorks), we can do the work for you, or we can support your engineering group’s efforts.
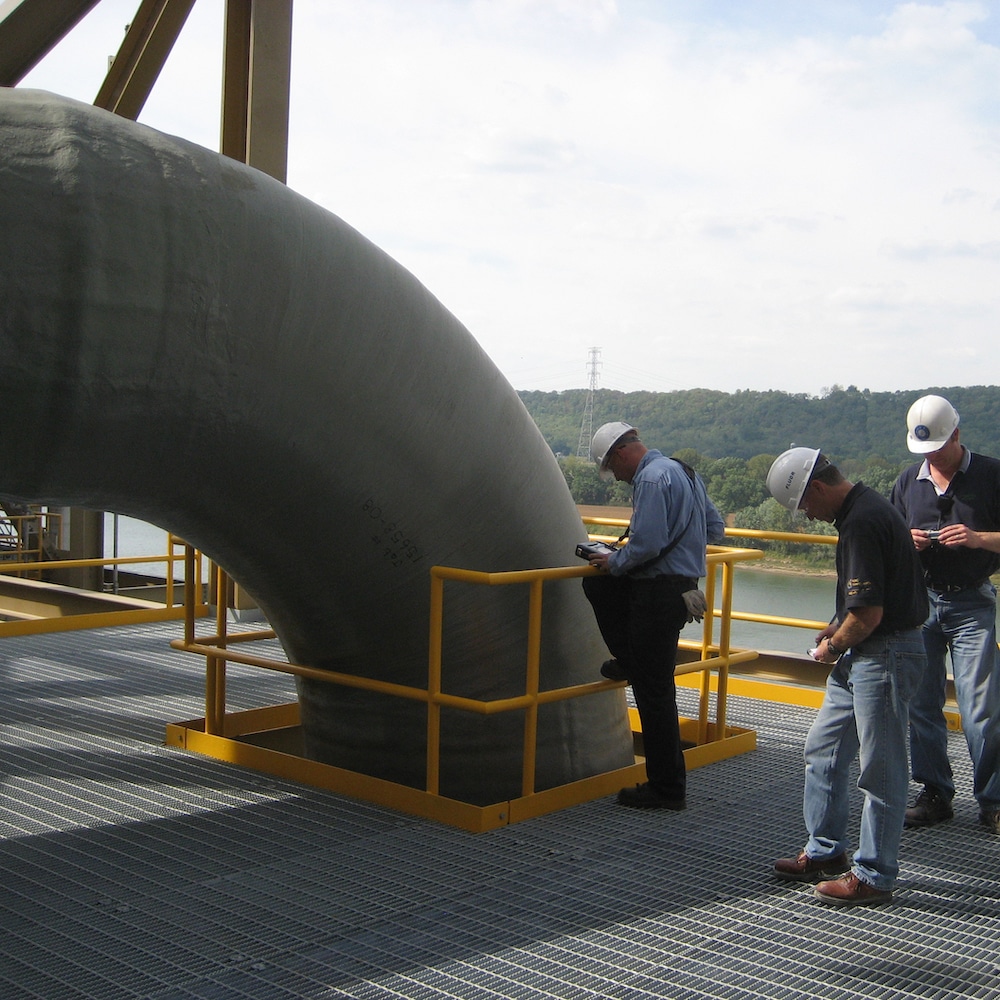
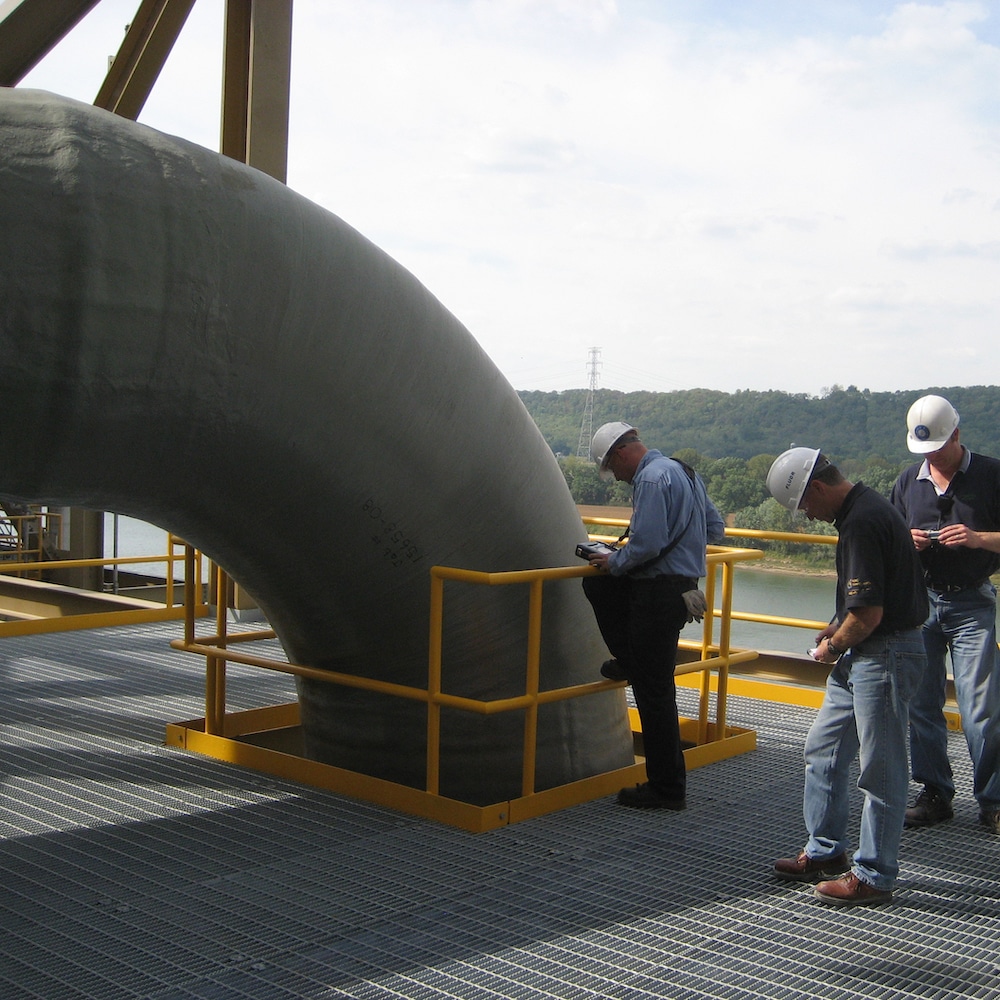
On Site Inspection and Repair Recommendation
RPS engineers and technicians provide onsite inspection services of installed composite equipment and make repair recommendations to extend service life. Composite equipment can have a 50+ year life expectancy in many industrial applications. We also have the capability to inspect your FRP composite equipment while it’s still in service.
Regular inspection and maintenance will help ensure you realize the maximum life expectancy of your composite equipment.
Contact us to find out how our Engineering department can support your next project.